CHARACTERISTICS AND COMMON VULNERABILITIES INFRASTRUCTURE CATEGORY: NUCLEAR FUEL CYCLE SAFETY AND SECURITY
- 18 pages
- Draft
- Law Enforcement Sensitive
- Sensitive Homeland Security Information
- February 13, 2004
NUCLEAR FUEL CYCLE CHARACTERISTICS
Nuclear power plants in the U.S. use fuel rods that have been enriched in the uranium-235 (235U) fissile isotope. At the time of their insertion to the reactor, typical commercial power plant fuel rods contain approximately 2% to 5% 235U; the exact value depends on the details of the reactor design. This fuel remains in the reactor for up to three years or more, at which time fission product buildup necessitates its removal even though it still contains significant quantities of 235U.
The entire nuclear fuel cycle contains several components as illustrated schematically in
Figure 1. The Nuclear Regulatory Commission (NRC) has the overall regulatory responsibility
for the safety and security of commercial nuclear power plants and the associated nuclear fuel
cycle facilities in the U.S. This responsibility has included ensuring that licensed nuclear
facilities provide safety and security against sabotage and theft of nuclear materials.Uranium Mining and Milling
Until about ten years ago, uranium was typically mined in surface mines (open cut mines) and
deep shaft mines. More recently, however, in-situ leaching in which chemical solutions are
injected into underground uranium deposits to dissolve uranium has become more widely used.Each technique concentrates the uranium into a product known as “yellowcake” (uranium oxide
[U3O8]) because of its yellowish color.The mined yellowcake is trucked to a milling facility where it is crushed and leached. In most
cases, sulfuric acid is used as the leaching agent, but alkaline leaching can also be used. The
leaching agent not only extracts uranium from the ore, but also several other constituents,
including vanadium, selenium, iron, lead, and arsenic.Conventional mills crush the ore and extract 90% to 95% of the uranium. Mills are typically
located in areas of low population density, and they process ores from mines within about
50 kilometers (30 miles) of the mill. Approximately 21 uranium milling facilities are licensed by
the NRC. However, as of September 2003, most of these mills are in decommissioning, three are
in stand-by mode, and only one is in operation. This status reflects several market issues,
including the inventory of mined and milled uranium, the flat demand curve for enriched
uranium in the U.S., and the availability of enriched uranium from overseas suppliers.Conventional mills crush the ore and extract 90% to 95% of the uranium. Mills are typically
located in areas of low population density, and they process ores from mines within about
50 kilometers (30 miles) of the mill. Approximately 21 uranium milling facilities are licensed by
the NRC. However, as of September 2003, most of these mills are in decommissioning, three are
in stand-by mode, and only one is in operation. This status reflects several market issues,
including the inventory of mined and milled uranium, the flat demand curve for enriched
uranium in the U.S., and the availability of enriched uranium from overseas suppliers.NRC requirements for uranium mills cover the control of industrial hazards and address waste
and decommissioning concerns. Because the uranium in the milling facilities is not enriched, no
criticality hazard, and little fire or explosive hazard, exists for the uranium. However, the solvent
extraction process does present a fire hazard. The primary hazards associated with milling
operations are occupational hazards found in any metal milling operation that uses chemical
extraction, plus the chemical toxicity of the uranium itself. Radiological hazards are low at these
facilities, as uranium has little penetrating radiation and only moderate non-penetrating radiation.
The primary radiological hazard is due to the presence of radium in the uranium decay chains
and the production of radon gas from the decay of radium and radon progeny (short-lived radon
decay products).The solid waste from the milling process is called mill tailings. These tailings, which contain
most of the progeny of uranium, are a significant source of radon and radon progeny releases to
the environment. Human risks involve inhalation of radon progeny that may be deposited in the
respiratory tract. Alpha radiation would be emitted into those tissues and could pose a cancer risk
to anyone who inhales radon progeny.Uranium Conversion
The next stage in the nuclear fuel cycle is conversion of the milled U3O8 into pure uranium
hexafluoride (UF6) gas for use in the enrichment stage. During the conversion stage, impurities
are removed from the U3O8, and the uranium is combined with flourine to create the UF6 gas that
is then pressurized and cooled to a liquid. In its liquid state, it is drained into 14-ton cylinders
where it solidifies after cooling for approximately five days. After cooling, the UF6-containing
cylinder is shipped to an enrichment plant.The NRC has licensed the Honeywell International, Inc., Conversion Facility in Metropolis,
Illinois. This is the only operating conversion facility in the U.S. Other countries having
conversion plants are Canada, France, United Kingdom, China, and the Russian Federation.
As with mining and milling, the primary risks associated with the conversion process are
chemical and radiological. Strong acids and alkalis are used in the conversion process, which
involves converting the yellowcake (uranium oxide) powder to very soluble forms, leading to
possible inhalation of uranium. In addition, conversion produces extremely corrosive chemicals
that could cause fire and explosion hazards.On December 21, 2001, the NRC notified Honeywell International, Inc., that interim security
enhancements must be implemented “… to provide the Commission with reasonable assurance
that the public health and safety and common defense and security continue to be adequately
protected in the current threat environment.” On March 25, 2002, the NRC formalized these
interim enhancements in the form of an NRC Order. Details of the enhanced security
requirements at Honeywell International, Inc., are not publicly available.…
Share this:

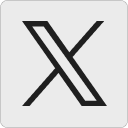


